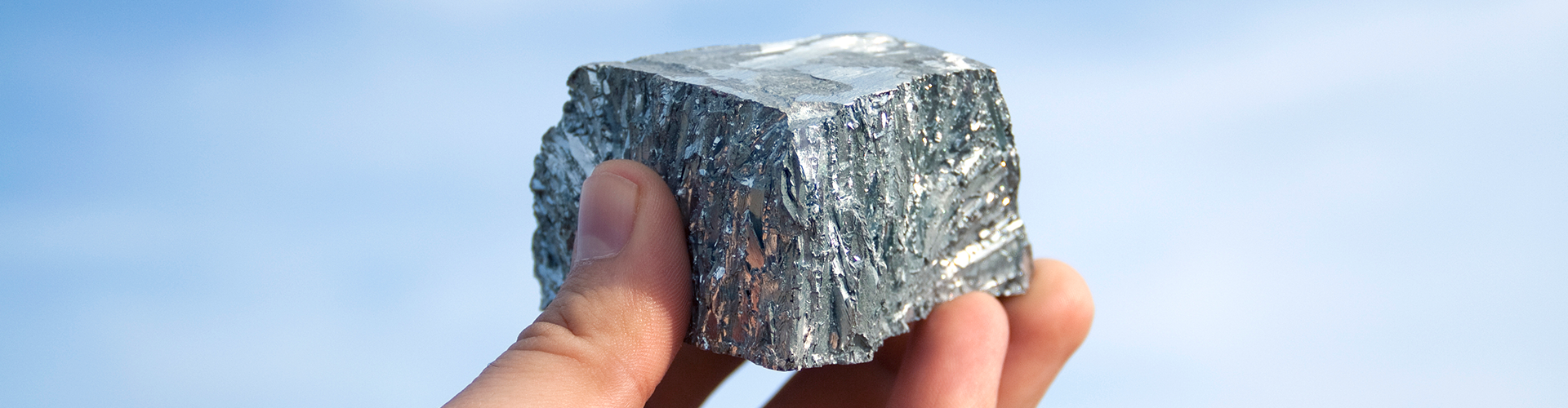
Surface treatment
There are different types of surface treatments, all with different goals. Surface treatments are methods of making products or materials meet certain desired criteria. For example, to counteract wear and corrosion or to obtain a surface with a special aesthetic. One method does not exclude the other and so there are several possible combinations, each combination having unique properties.
Hot dip galvanizing
Hot dip galvanizing is one of the most effective methods to protect from corrosion. The method results in an almost maintenance free product during the whole lifetime. Already in 1741, the French chemist Melouin discovered that zinc can protect steel against corrosion. However, it took until 1837 before the method started to be used. It was the engineer Sorel that patented a method to use ammonium chloride as flux.
Why does Eurostair® use hot dip galvanizing?
Our products are used both outdoors and indoors. Products outdoors are in different degrees exposed to weather and affected by the climate, but products need to be protected even in indoor environments. Especially within industries it is usually demanding environments. Eurostair®’s products should always have the highest quality, have a well-thought out construction and give more value, including for our environment. Hot dip galvanizing is the method that gives our products the highest protection against corrosion with a low environmental impact.
Method for hot dip galvanizing
Before the material is about to hot dip galvanize it is carefully cleaned from fat, oil, rust, and other filths. This is done by chemical baths that cleans the steel. Further on the material is washed before it is immersed in a pot of hot zinc with a temperature of around 460 °C. This method gives a strong metallic bond between the steel and the zinc which ensures sustainability and creates a cathodic protection. If there would be any micro areas not covered by zinc the cathodic protection will fill this area by itself. As a method the hot dip galvanization created a durable and resistant surface with a long lifespan and is essentially maintenance free.
Description of the process
The process for hot dip galvanization is carefully controlled. First a degreasing and pickling takes place to erase all fat areas, contaminations and welding residues. Further on the material is carefully washed. After the material is dried it is immersed into the zinc bath. Since zinc has an open structure it can bind with the steel surface. In this moment, a joining on a molecular level takes place which gives the strong and effective protection. After cooling the material is inspected and controlled to ensure the desired result.
For more information about hot dip galvanization and meticulous description about the process we recommend Nordic Galvanizers site.
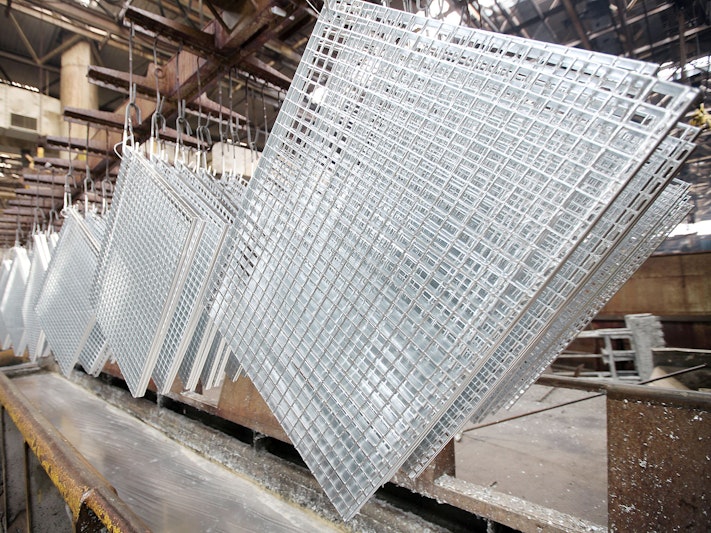
Straight and spiral staircases made of high strength steel, with easy and quick assembly.
From one of the leading staircase manufacturers in Europe.
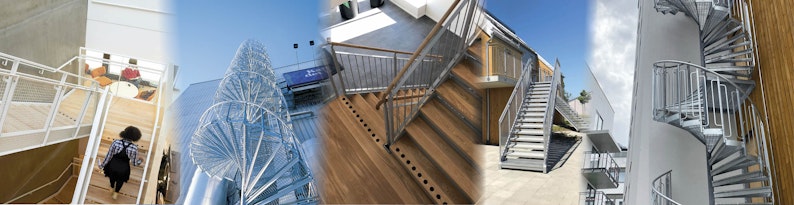

Powder coating
Solely powder coating as surface treatment should only be used for products that are placed indoors. Powder coating is a durable, protective, and environmentally friendly method for surface treatment method. Compared to traditional painting which consists of much solvent the powder coating is much less polluting. The method can be used to paint many types of material. As color surface the powder coating is enduring and handle both mechanical strains and strong chemicals. The application is done in a dry and electronic way which facilitates an even distribution of the color particles and it is easy to access hidden angles. Powder coat the staircase in optional RAL color. We have the most common colors in stock.
Why does Eurostair® use powder coating?
Eurostairs® products should always be of highest quality, have a well-thought out construction and give more value, including to the environment. Powder coating is a very environmentally effective treatment. Color is applicated without any solvent and gives minimal overspray. Today this is the leading method to paint in an environmentally friendly way. It is also the best painting method when it comes to work environment. The people working with powder coating do not have to stand in a cloud of solvent. For us at Eurostair®, powder coating is the obvious choice.
Methods for powder coating
Painting with powder coating offers an unlimited choice of color with a very good color match. Powder coating is the dominating painting method today. Powder coating is done with polyester powder with a layer thickness of approximately 60 my. There are not any limitations when it comes to colors. Today we can paint with the whole RAL-scale but also NCS-S if you prefer. It is important to state the gloss when you chose color. Eurostair® recommend gloss between 80-30 where 80 in blanc and 30 is matt.
Description of the process
To get the right quality of the painted surface it is important with both pretreatment and application of the coat as the following hardening. Since you want to achieve maximal adhesion and sustainability the pretreatment is crucial. The pretreatment normally consists of degreasing and grazing of the surface followed by a chrome free chemical treatment. The pretreatment ends when the material is washed in deionized water. The pretreatment gives the absolute best corrosion resistance and adhesion for products that should be used outdoors. The polyester powder is then applicated by an electrostatic or friction charge and afterwards the powder is hardening in an oven at minimum 180 ºC. Powder coat is applicated and hardened without any solvent. The ventilation air from the powder application is cleaned in effective purifications. The powder that misses the material is taken care of in a recycling system and reversed to the spray gun.
Duplex treatment
Duplex treatment is recommended mainly for painted products outdoors. Hence, duplex treatment can also be needed if the product should be placed indoors in a humid or corrosive environment. Duplex treatment, i.e. both hot dip galvanization and powder coating, gives a very good corrosive protection since the underlying zinc prevents from corrosion even if the paint layer is damaged, for example in transportation or assembly. A duplex treatment gives a surface treatment with a low lifetime cost. The method is slightly expensive initially but on the other hand the maintenance and replacement costs are substantially lower. Powder coat the staircase in optional RAL-color.
Why does Eurostair® use powder coating?
We use duplex treatment on a painted staircase that should be placed outdoors or if a painted staircase should be placed indoors in a corrosive environment. Eurostair®’s duplex treatment means that we perform surface treatment in two steps, first a hot dip galvanization followed by powder coating. Hot dip galvanization gives the product a long lifespan and effectively protects against corrosion. The powder coating is an environmentally effective painting method with highest quality for both indoor and outdoor use. For us at Eurostair® a duplex treatment is the obvious choice for a painted product which should have the highest protection against corrosion.
Methods for duplex treatment
In our duplex treatment we merge two effective surface treatments. Hot dip galvanizing is one of the most effective methods for corrosion protection available. Hot dip galvanization according to the norm EN 1461 is completely maintenance free during the whole lifespan. Zinc is a basic metal compared to steel and therefore minor damages in the zinc coating will be cathodically protected and therefore does not need to be repaired. Outside of this corrosion protection we then applicate powder coating. Powder coating is done with polyester powder with a layer thickness of approximately 60 my. There are not any limitations when it comes to colors. Today we can paint with the whole RAL-scale but also NCS-S if you prefer. It is important to state the gloss when you chose color. Eurostair® recommend gloss between 80-30 where 80 in blanc and 30 is matt.
Description of the process
It is essential that the pretreatment and the hot dip galvanization is performed according to the right process. To adhesion and sustainability should work the pretreatment is completely crucial. When the hot dip galvanization has gone through the first step and dried the material is ready to be powder coated with polyester powder. The powder is applicated on the material by electrostatic or friction charge and afterwards the powder is hardening in an oven at minimum 180 ºC. During the process ventilation air from the powder application is cleaned in effective purifications. The powder that misses the material is taken care of in a recycling system and reversed to the spray gun.
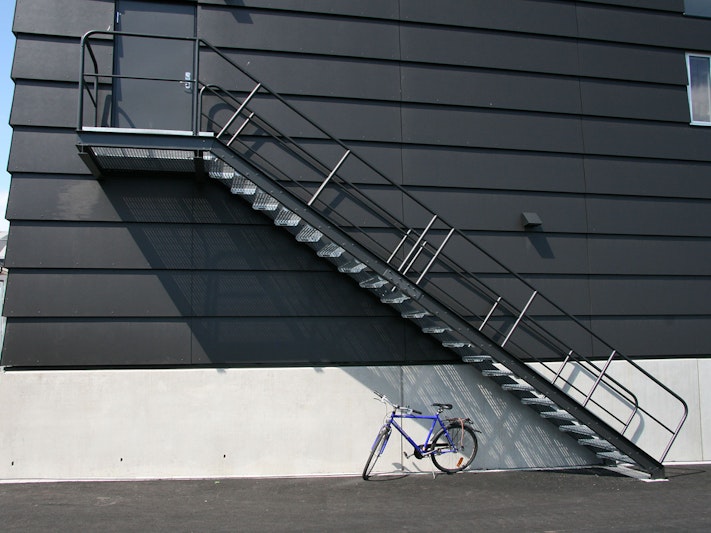
Straight staircases made of high strength steel, with easy and quick assembly.
From one of the leading staircase manufacturers in Europe.
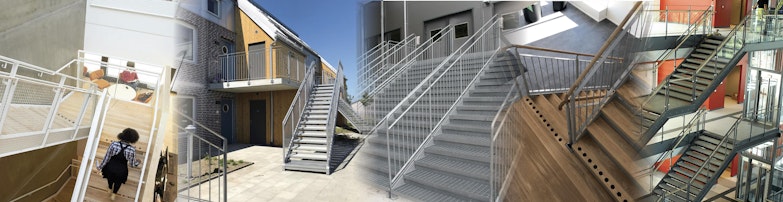
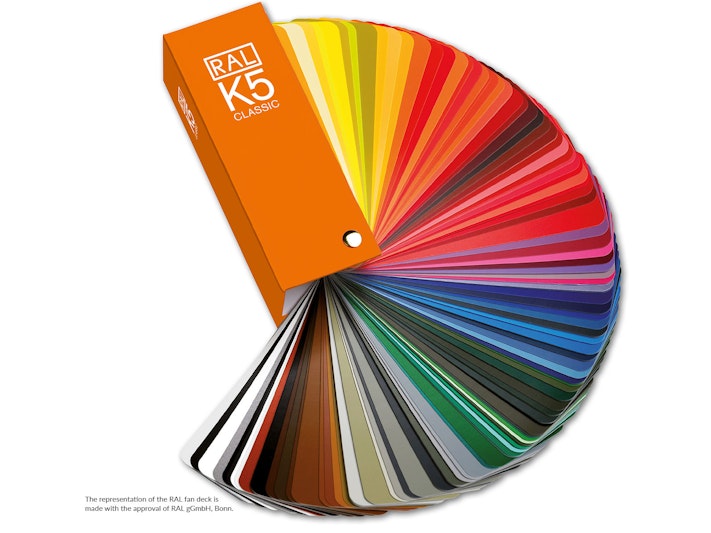
RAL colors
Eurostair® has chosen RAL Classic® to offer colour-stable industrial colours.
From the 215 shades of the RAL scale, 18 colors were selected as the standard color for our products.
Optionally, we can paint your product in any desired color.
WHY DID WE CHOOSE RAL AND NOT NCS?
RAL Classic is a color collection that is mainly based on the requirements of industry. These colors are based on a standardized four-digit color code.
RAL has set a number of criteria for creating an industrial color scale.
- The color must be of overriding public interest and not a matter of fashion.
- The color must have a certain minimum distance to existing ones.
- The commercially available pigments, which are not proven to be environmentally hazardous, must be able to be tinted.
- With a few exceptions, the color must have good opacity on "black and white".
- The color must be able to be produced in such a way that good wear resistance is guaranteed.
- Since our products often have to interact with other details to form a whole, we rely on the RAL color system to ensure high quality.
GLOSS, GLOSS
High gloss 80 ≤ x <90 at 60° angle
Satin 35 ≤ x <60 at 60° angle
What do the different gloss values look like? You can say that shiny is 80 - 95* gloss value.
Satin corresponds to 63 - 77 * gloss value. To obtain an evenly matt color, the gloss level is 20 - 30*.
(* Gloss according to ISO 2813/60° angle)
Our standard colors
Eurostair® offers a quality color system by using the standard RAL Classic®. We have selected 18 colors that are Eurostair® Standard colors to match the industry's standard colors. As an option, we can paint any RAL color you wish, there are 215 different colors to choose from.
RAL 1003
Eurostair® yellow
RAL 9010
Pure white
RAL 9016
Traffic white
RAL 9003
Signal white
RAL 7035
Light grey
RAL 7042
Traffic grey
RAL 7024
Graphite grey
RAL 7016
Anthracite grey
RAL 2003
Pastel orange
RAL 3002
Carmine red
RAL 3009
Oxide red
RAL 8004
Copper brown
RAL 5024
Pastel blue
RAL 5010
Gentian blue
RAL 5000
Violet blue
RAL 9005
Jet black
RAL 6024
Traffic green
RAL 6027
Light green